Vita | Manager |
info@thespecialtrucks.com
Clw Inc.| No.1 special truck manufacturers in China | https://thespecialtrucks.com
Experience the Clw Inc. Difference - Visit Our State-of-the-Art Factory!
See firsthand our innovative manufacturing process and commitment to quality. Schedule your factory tour today:
info@thespecialtrucks.com
company catalogue

Have you ever wondered how the trucks and vans that keep our world moving are designed, built, and constantly improved? The answer often lies in a detailed understanding of specifications, needs, and the clever application of engineering principles. **WI** plays a vital role in this, ensuring that these vital vehicles are not only safe and reliable but also perfectly suited for the diverse range of tasks they perform. This article explores the intricate details of this field within the vans and truck manufacturing industry, offering insights that will empower you to better understand the vehicles that often go unnoticed but are the driving force behind our economy.
Understanding the Core Principles of WI in Manufacturing
At its heart, WI represents a systematic method within the manufacturing sector, meticulously crafted to ensure the seamless flow of operations and the consistent delivery of high-quality products. Imagine the intricate process of building a truck – from the initial design to the final assembly. WI acts as a blueprint, guiding every step with clarity and precision. This process is all about defining clear, step-by-step procedures for each task. This means everyone involved knows exactly what to do, how to do it, and when to do it. Think of it like a well-organized recipe, ensuring every dish (or in this case, every truck or van) comes out perfectly every single time. This structured foundation is crucial for enhancing efficiency, minimizing errors, and maintaining consistently high standards across the entire production journey. Let’s delve deeper into the core components that make this process successful.
- Standardization: Establishing uniform procedures for all operations.
- Documentation: Creating comprehensive records for reference and training.
- Continuous Improvement: Regularly evaluating and refining procedures for better outcomes.
The advantages are clear: improved productivity, reduced waste, and enhanced product quality. By adopting this systematic approach, manufacturers can ensure that their processes aren’t just efficient, but also adaptable and resilient, allowing them to respond effectively to evolving market demands and challenges. This isn’t merely about following a set of rules. It involves fostering a culture of continuous learning and innovation, empowering workers to contribute their insights and expertise toward improving the manufacturing process. This collaborative element is essential for sustaining the long-term success and competitiveness of any manufacturing enterprise. Consider, for instance, the assembly line for a Fuel Truck – 12.6m³ Diesel Engine. WI would dictate the specific tools, torque settings, and inspection criteria for each stage, minimizing the risk of errors and safety hazards.
The Role of WI in Ensuring Quality Control
Quality control is not just a process; it’s a commitment to excellence. In the vans and truck manufacturing industry, this means ensuring every vehicle that rolls off the assembly line meets the highest standards of safety, performance, and reliability. Now how Does WI help? Think of WI as the guardian of quality. It provides the detailed procedures and checklists that quality control inspectors use to meticulously examine every aspect of a vehicle, from the engine to the tires. Here’s a closer look at how it helps:
- Inspection Standards: Detailed guidelines for inspecting all components and systems. This is where you’d check for anything from faulty wiring to incorrect paint application.
- Testing Protocols: Specific procedures for testing vehicle performance, such as braking efficiency and engine power. These tests make sure that the vehicle works the way it’s supposed to.
- Documentation: Records of all inspections and tests, providing a clear audit trail. This documentation helps keep track of any problems and makes sure they’re fixed correctly.
Without clearly defined procedures, quality control can become inconsistent and ineffective. When quality control is inconsistent, problems might be missed and standards might be lower than they should be. By providing a standardized framework, the process reinforces a culture of accountability, ensuring that every member of the team recognizes their role in upholding quality standards. This helps to discover defects early on, preventing costly recalls and ensuring customer satisfaction. For example, the WI documentation related to the Explosive equipment transport truck would outline the stringent checks required for safety features like the explosion-proof cargo area and fire suppression system.
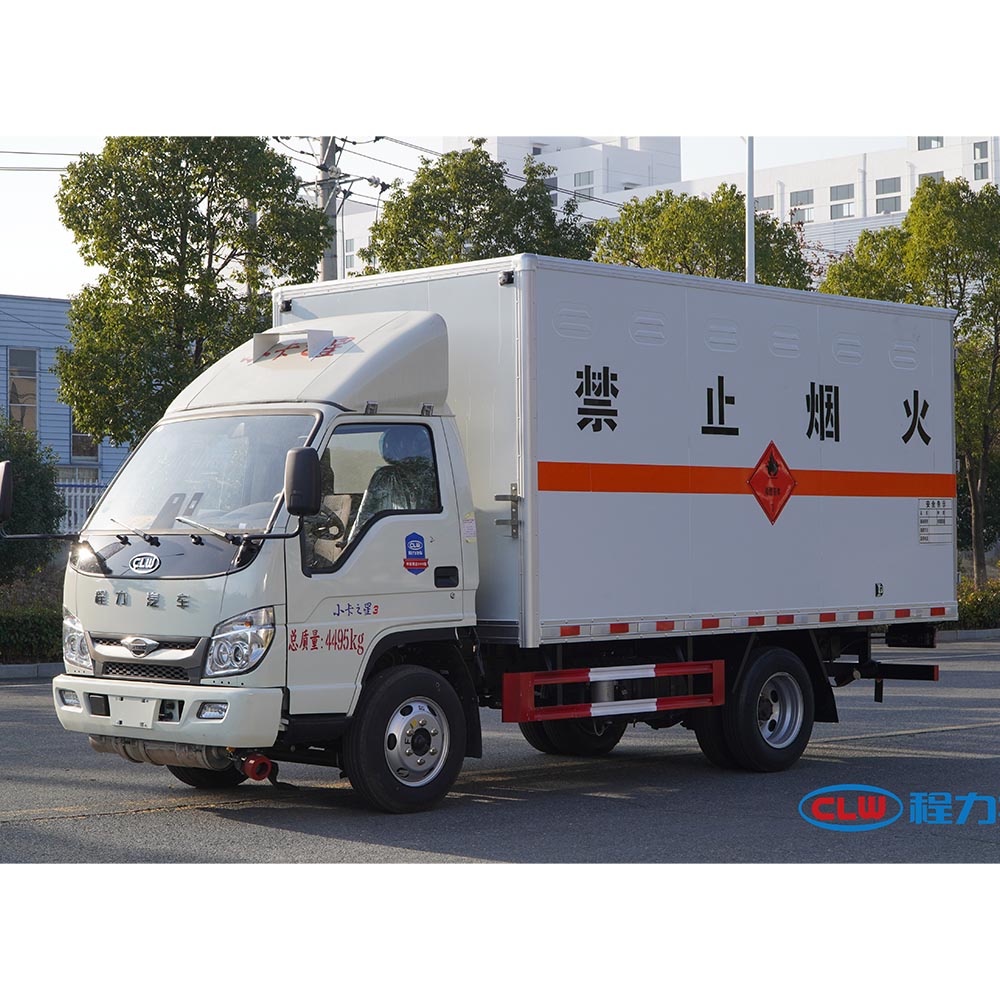
Streamlining Production with Standardized Procedures
Imagine an assembly line where each worker is doing things their own way. Chaos, right? Now, picture a well-oiled machine where everyone knows exactly what to do, when to do it, and how it should be done. That’s the power of standardized procedures created from WI. These procedures provide a clear and consistent roadmap for every step of the manufacturing process. They can help in several key ways:
- Reducing Variation: Minimizing inconsistencies in production processes, leading to uniform products. This means every truck or van that comes off the line is the same high quality.
- Improving Efficiency: Optimizing workflow and eliminating unnecessary steps. This can speed up production and save time and money.
- Enhancing Training: Providing a clear and structured framework for training new employees. New workers can learn the right way to do things quickly and easily.
Standardized procedures are not about stifling creativity or innovation. They are about establishing a baseline of best practices that can then be continuously improved upon. By streamlining processes and eliminating guesswork, manufacturers can significantly increase their output, reduce costs, and improve the overall efficiency of their operations. These detailed instructions make sure that everyone follows the same processes. Think of a vehicle like the Multifunctional Dust Suppression Truck 7m³ tank, 140HP engine. WI processes are standardized for manufacturing which will ensure consistent performance and reliability.
Optimizing Maintenance and Repair Processes Through WI
Beyond manufacturing, the principles of WI also apply to the maintenance and repair of vans and trucks. These work instructions provide mechanics with the detailed guidance they need to perform repairs efficiently and effectively. Consider maintenance – a well-defined WI process ensures that routine tasks like oil changes, tire rotations, and brake inspections are performed on time and to the correct standards. This proactive approach not only extends the lifespan of the vehicle but also helps prevent more serious and costly issues from arising. The process also helps reduce downtime, ensuring that vehicles remain operational and productive. Here are some key applications:
- Routine Maintenance: Providing step-by-step instructions for all scheduled maintenance tasks. Think of changing oil or rotating tires.
- Diagnostic Procedures: Guiding technicians through troubleshooting steps to identify and resolve issues. Helping them figure out what’s wrong with the vehicle.
- Repair Instructions: Offering detailed instructions for specific repairs, including part replacements and system overhauls. Guiding them in fixing what’s not working.
With clear instructions and standardized procedures, maintenance and repair teams can work more efficiently, reduce errors, and minimize downtime. WI can be used to build maintenance schedules, diagnostic protocols, and repair procedures. This enables a more proactive and efficient approach to vehicle upkeep. Using a standardized process for maintaining a Top-Quality Wrecker, WI would specify the correct lubricants, torque settings, and inspection intervals to ensure its continuous readiness for roadside assistance.
The Role of Technology in Supporting WI Implementation
In today’s digital age, technology plays a vital role in supporting the implementation and management of WI. Digital platforms and software solutions enhance accessibility, collaboration, and real-time updates, ensuring that everyone has the information they need, when they need it. Here are some ways in which technology can enhance the effectiveness of WI:
* Digital Documentation: Replacing paper-based instructions with easily accessible electronic documents. No more bulky manuals!
* Interactive Training: Using multimedia tools and simulations to enhance learning and retention. Making training more engaging and effective.
* Real-Time Updates: Providing immediate access to the latest revisions and updates. Keeping everyone on the same page with the most current info.
These are not just static documents. Digital platforms enable real-time updates, annotations, and feedback, fostering a culture of continuous improvement and collaboration. Technology can also provide real-time performance data, allowing managers to identify bottlenecks, track progress, and make data-driven decisions to optimize operations. This integration of technology transforms WI from a set of static instructions to a dynamic and collaborative system that adapts to the ever-changing needs of the manufacturing environment. Imagine a technician using a tablet to access the WI for a complex repair on an Chengli Dongfeng D9 intelligent asphalt distributor. The tablet could provide interactive diagrams, video tutorials, and even connect them with remote experts for assistance.
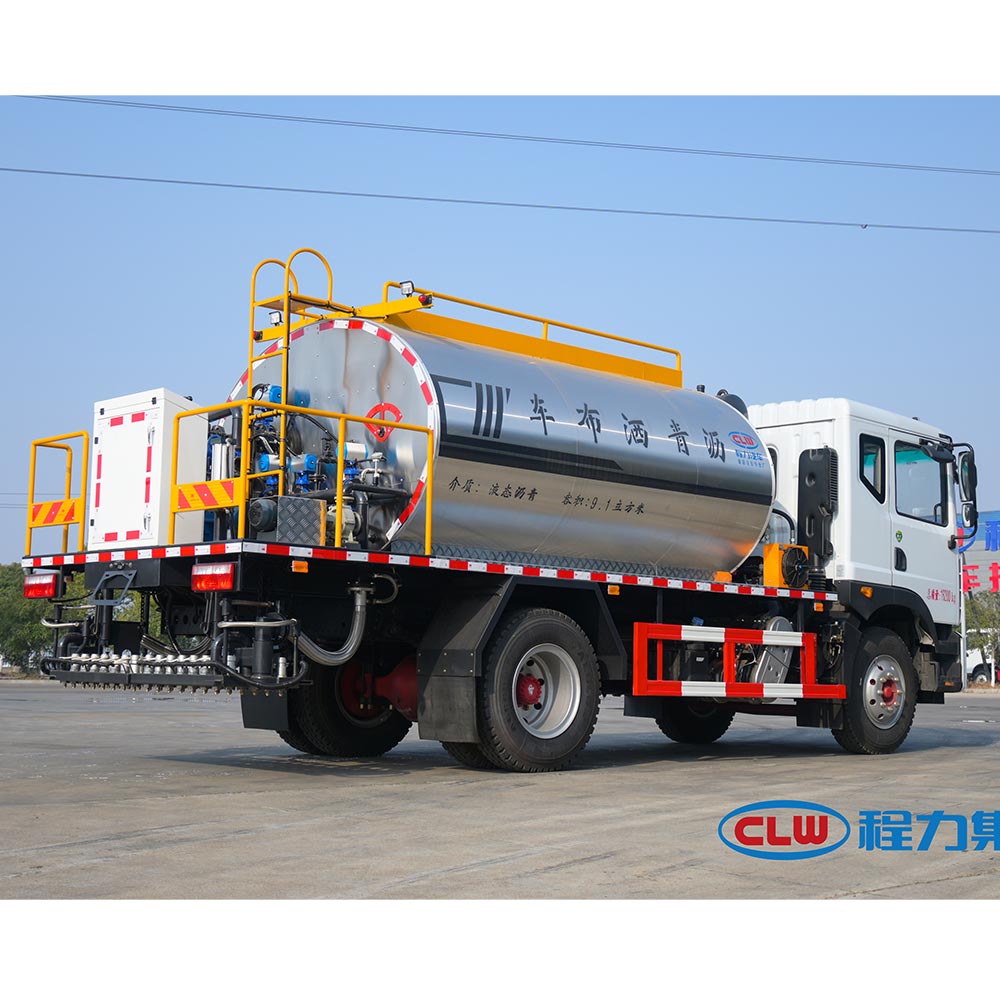
Benefits of Embracing WI for Employee Training
Investing in employee training is an investment in the future. By providing employees with the knowledge and skills they need to excel, you not only improve their individual performance but also contribute to the overall success of the organization. WI are the perfect tool for empowering your workforce. It ensures that everyone receives consistent, standardized training, regardless of their experience level or background. Here are some things to consider:
- Standardized Training: Ensuring all employees receive consistent information and instruction.
- Accelerated Learning: Providing a clear and structured framework for faster knowledge acquisition.
- Reduced Errors: Minimizing mistakes and rework through clear and comprehensive guidelines.
WI not only improves the quality of training but it also reduces the time and resources required to bring new employees up to speed. For example, new recruits working on the assembly line for a Greening Spraying Truck can quickly learn the correct procedures for installing nozzles and pumps by following step-by-step instructions accompanied by visual aids.
Creating User-Friendly WI Documents
WI will only be effective if they are easy to understand and use. Clear, concise, and visually appealing documents are essential for ensuring that employees can quickly access the information they need and apply it correctly. Think about these things when creating WI documents:
* Simple Language: Using straightforward language and avoiding technical jargon.
* Visual Aids: Incorporating diagrams, illustrations, and photographs to enhance understanding.
* Step-by-Step Instructions: Breaking down complex tasks into manageable steps.
By following these guidelines, you can create WI documents that are not only informative, but also engaging and user-friendly. These documents serve as invaluable resources, empowering employees to perform their tasks with confidence and precision. A well-designed WI might use exploded diagrams and numbered steps to show how to replace a brake pad on a JAC high-end refrigerated truck.
WI for Enhancing Safety Protocols in Truck Manufacturing
In the demanding world of vans and truck manufacturing, safety isn’t just a priority; it’s a core principle. It’s about protecting workers, preventing accidents, and ensuring a secure working environment for everyone. How does WI help with safety? They guide employees on the correct use of equipment, the handling of hazardous materials, and adherence to safety regulations. Here’s how WI contributes significantly to enhancing safety protocols:
- **Equipment Operation**: Providing detailed instructions on the safe and proper use of machinery and tools.
- **Hazardous Materials Handling**: Outlining procedures for handling and storing hazardous materials safely.
- **Emergency Procedures**: Clearly displaying emergency procedures and evacuation plans.
These protocols are not suggestions; they are essential for maintaining a safe working environment. It ensures that every employee knows what to do in any given situation. This preparedness can save lives and prevent injuries. Specific to the manufacturing safety standards for a Pure Electric Garbage Truck, the WI would emphasize safety protocols related to high-voltage components and battery handling. Because they reduce the risk of accidents and injuries, WI’s not only protect employees but also contribute to a more productive and efficient work environment.
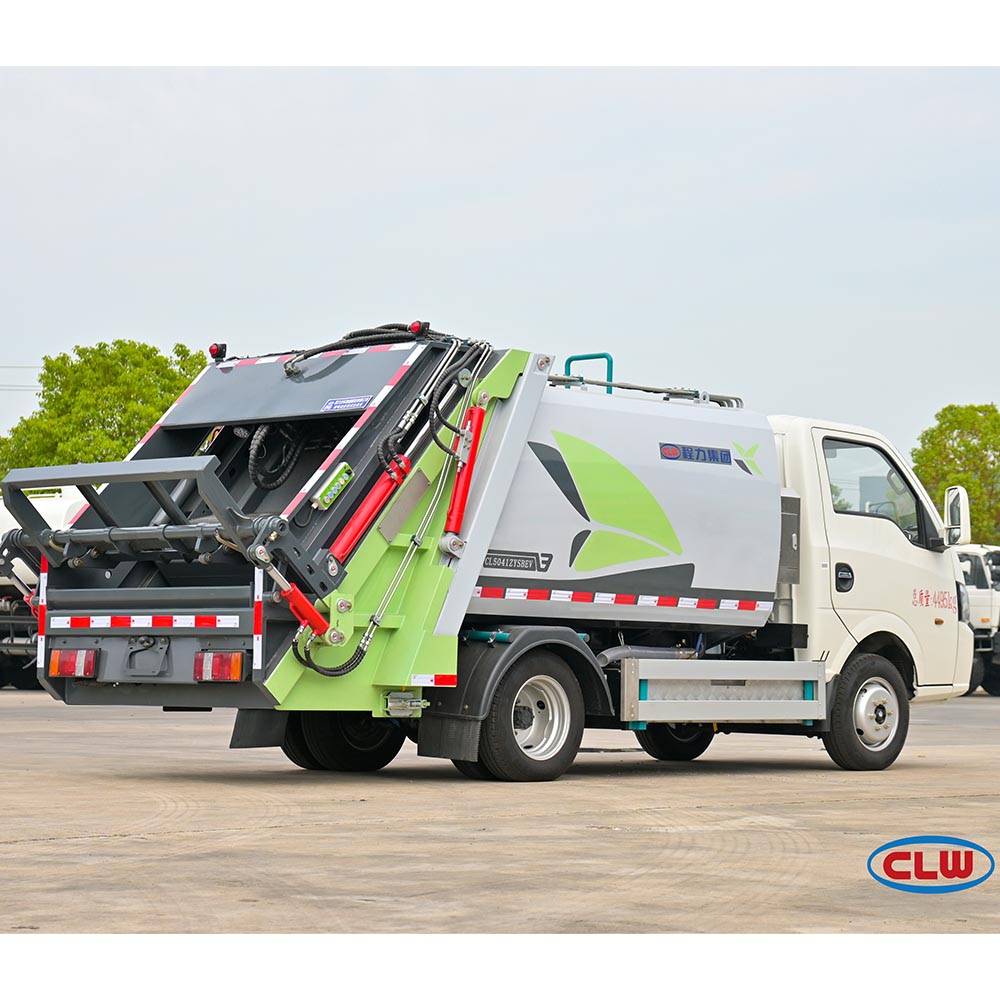
Adapting WI to Different Manufacturing Environments
The great thing about this is how flexible it is! It isn’t a one-size-fits-all solution. It can be customized to effectively address distinct requirements, conditions, and constraints in differing manufacturing environments. Whether you’re running a high-volume assembly line or a small-scale custom shop, the principles of WI can be adapted to suit your specific needs. Consider these flexible steps:
- **Assess Specific Needs**: Evaluate the specific goals and operational processes of each manufacturing setting before implementing WI.
- **Customized Procedures**: Adjust WI to fulfill diverse industry standards, equipment types, and workforce abilities.
- **Continuous Feedback**: Gather and incorporate input from employees at all levels to optimize WI regularly for maximum relevance and impact.
This flexibility enables organizations to effectively apply WI concepts to their respective operational contexts, enhancing effectiveness and encouraging widespread acceptance. Take a maintenance shop specializing in Flammable gas transport vehicle. Here, the WI would need to be adapted to address the specific safety regulations and specialized repair procedures associated with those vehicles.
The Future of WI in the Vans and Truck Industry
As technology continues to advance, the role of WI in the vans and truck manufacturing industry will only become more important. Emerging technologies like artificial intelligence, augmented reality, and the Internet of Things will revolutionize the way WI is created, delivered, and utilized. These advances will help to create more efficient processes within manufacturing.
- **AI-Powered WI**: AI algorithms can analyze production data to identify areas for improvement and automatically generate optimized procedures.
- **AR-Enhanced Training**: Augmented reality can overlay digital information onto real-world environments, providing employees with hands-on guidance and training.
- **IoT-Connected Processes**: The Internet of Things can connect machines, sensors, and other devices, providing real-time data and insights that can be used to improve decision-making.
These technologies promise to transform WI from a static set of instructions to a dynamic and intelligent system that continuously learns and adapts to the ever-changing needs of the manufacturing environment. They’re not a futuristic concept, but rather a current revolution that will enhance operations and improve overall efficiency and product delivery.
Addressing Common Challenges in WI Implementation
The implementation of WI is undoubtedly advantageous, but hurdles persist. Common setbacks might involve employee resistance, the need for regular updates, and alignment with operational goals to make the most of them: Overcoming these issues involves a multifaceted plan:
* **Gaining Employee Buy-In**: By involving employees early, you can foster a feeling of ownership and responsibility, making them more likely to embrace the new system.
* **Ensuring Regular Updates**: Establish a system for frequently assessing and updating documents to represent modifications in protocols, equipment, and regulations.
* **Aligning with Business Objectives**: Make sure WIs align with the overall goals and objectives of the organization, promoting process improvement.
These tactics assist overcome obstacles to implementation and ensure WI’s successful integration, which eventually strengthens operational efficiency and standardization. These tips ensure WI is practical, applicable, and effective in accomplishing its objectives in various sectors and industries.
Measuring the Success of WI Initiatives
How do you know if its working? Tracking the effectiveness of WI projects is necessary for improving results. Key Performance Indicators, or KPIs, give you metrics to assess effectiveness, boost the usage, and validate positive influence on overall operations.
- **Improved Efficiency Metrics**: Track changes in production times, error rates, and employee productivity pre- and post-implementation.
- **Employee Feedback**: Use surveys, interviews, and performance statistics among staff workers to assess involvement and comprehension.
- **Quality Control Results**: Consistently monitor consistency in product quality and declines in defects or recalls to confirm efficiency.
Use these steps to ensure that WI tactics are successful, have a positive impact on business, and remain optimized by regular assessment and modification depending on new data!
Inspiring a Culture of Continuous Improvement with WI
WI shouldn’t be seen as a static set of rules. It should be viewed as a living document that evolves and improves over time. You can encourage a mindset of continuous improvement by encouraging employee feedback, conducting frequent audits, and embracing new technologies: Here’s some examples of strategies:
- **Involving Your Employees**: Encourage employees to provide consistent input and ideas for enhancing it.
- **Conducting Frequent Audits**: Check and evaluate it with a predetermined regularity to find gaps and possibilities for improvement.
- **Embracing New Technologies**: Integrate new tools and technologies to streamline processes and enhance effectiveness.
These strategies create a culture of ongoing optimization, in which improvements are incorporated into everyday operations, resulting in greater efficiency, quality, and employee engagement. Always strive to make things better than they were before, for long run success.
FAQs About WI in the Trucking Industry
Still have questions? Let’s tackle some common ones:
How do I start implementing it in my truck manufacturing plant?
Start by identifying key processes, documenting current procedures, and creating clear, step-by-step instructions. Involve employees in the process to gain their buy-in and ensure the WI are practical and easy to follow.
What are the signs that my WI isn’t working effectively?
Look for signs like increased error rates, decreased productivity, employee resistance, and inconsistent product quality. These indicators suggest that the it needs to be revised or better communicated.
How often should I update my WI?
Update them regularly, especially when there are changes in equipment, processes, regulations, or employee feedback. Regular reviews every six months to a year are recommended.
Can WI help me reduce costs in my manufacturing process?
Absolutely. Clear, standardized procedures can minimize errors, reduce waste, improve efficiency, and lower training costs, leading to significant cost savings over time.
Are there any industry standards or regulations related to WI?
While there aren’t specific regulations, adhering to industry best practices such as ISO 9001 for quality management can guide your WI development and ensure compliance with broader standards.
How can I make it more engaging for my employees?
Use visual aids, interactive training methods, and clear, concise language. Encourage employee feedback and incorporate their suggestions into the process to foster a sense of ownership and collaboration. These methods will keep users engaged and improve the usability of the procedures.
Conclusion: WI – The Keystone of Truck Manufacturing Excellence
In summary, WI isn’t just a documentation exercise, it’s the backbone of streamlined and exceptional truck manufacturing. Integrating these guidelines into your processes allows for enhanced quality control, optimized maintenance, and a safer work atmosphere. As technology evolves, WI will undoubtedly become more intuitive and effective, but its core importance will endure as a cornerstone of operational excellence.
By embracing WI, manufacturers can achieve greater efficiency, reduce costs, and improve overall product quality, contributing to the continued success and growth of the industry and is essential for the smooth operation of many parts of manufacturing but its advantages extend deeply into vehicle maintenance. Now, armed with this knowledge, are you ready to harness the power of WI to drive your success in the competitive world of vans and truck manufacturing?