Vita | Manager |
info@thespecialtrucks.com
Clw Inc.| No.1 special truck manufacturers in China | https://thespecialtrucks.com
Experience the Clw Inc. Difference - Visit Our State-of-the-Art Factory!
See firsthand our innovative manufacturing process and commitment to quality. Schedule your factory tour today:
info@thespecialtrucks.com
company catalogue

Have you ever driven past a large warehouse and wondered about all those doors and trucks lined up? Those are loading docks, the unsung heroes of keeping our stores stocked and our economy moving! A crucial element of any efficient shipping and receiving operation involves the often-overlooked science of **Standard truck loading dock heights**. These heights are far from arbitrary; they’re the result of decades of standardization aimed at creating a seamless interface between trucks and facilities. Knowing all about this ensures smooth, safe, and quick loading and unloading.
Ever wonder why trucks can back right up to those docks without trouble? In this article, we’ll dive into the why’s and how’s of loading dock heights, exploring the standards, the variations, and the essential equipment that makes the whole process work.
So buckle up, and let’s learn about truck loading docks!
Why Standard Truck Loading Dock Heights Matter So Much
Imagine a world without standardized loading dock heights. Chaos would reign. Picture trucks struggling to align with docks, forklifts straining to reach goods, and packages tumbling to the ground. It’s a logistical nightmare, right? Standardizing these heights avoids all this confusion.
Think of it like this: it’s like having a universal language for trucks and warehouses. Everyone knows the rules, ensuring less time wasted, fewer accidents, and happier workers. It boils down to efficiency and safety. When you standardize, the time spent loading and unloading a truck is greatly reduced. This saves companies money and means products get to consumers quicker.
Safety is another huge benefit. When heights are standardized, there’s less chance of a forklift tipping over or a worker straining their back trying to lift something too high. It keeps everyone involved safer and healthier. Finally, standardization makes everything more cost-effective. Less damage to goods, faster turnaround times, and reduced labor costs all contribute to a company’s bottom line.
Let’s look at a quick example of how important standardization is.
Scenario | Without Standardization | With Standardization |
---|---|---|
Loading Time | 60 minutes | 30 minutes |
Accident Rate | 5% | 1% |
Damage to Goods | 3% | 0.5% |
As you can see, the benefits are clear. Standards create a safer, more efficient, and more productive environment for everyone involved.
Next time you see a truck smoothly backing up to a dock, remember all the unseen hard work behind the scenes!
The “Standard” Height: What You Need to Know
Alright, let’s get down to the nitty-gritty: what exactly *is* the standard height we keep talking about? Generally speaking, the most common **Standard truck loading dock heights** in North America hover around 48 inches (or 4 feet). This height works well for most semi-trucks and trailers, providing a comfortable transition for forklifts and other loading equipment.
However, it’s important to understand that this isn’t a hard-and-fast rule. Variations exist depending on the type of truck and the specific application. For example, smaller delivery trucks might require lower dock heights (more on that later). It’s also worth noting that in some regions, you might encounter slight variations based on local practices or historical factors.
Why 48 inches? Well, it’s a compromise developed over time to suit most vehicles. This height takes into account the average bed dimensions of trucks after considering elements of suspension. This height helps to ensure easy access and safety.
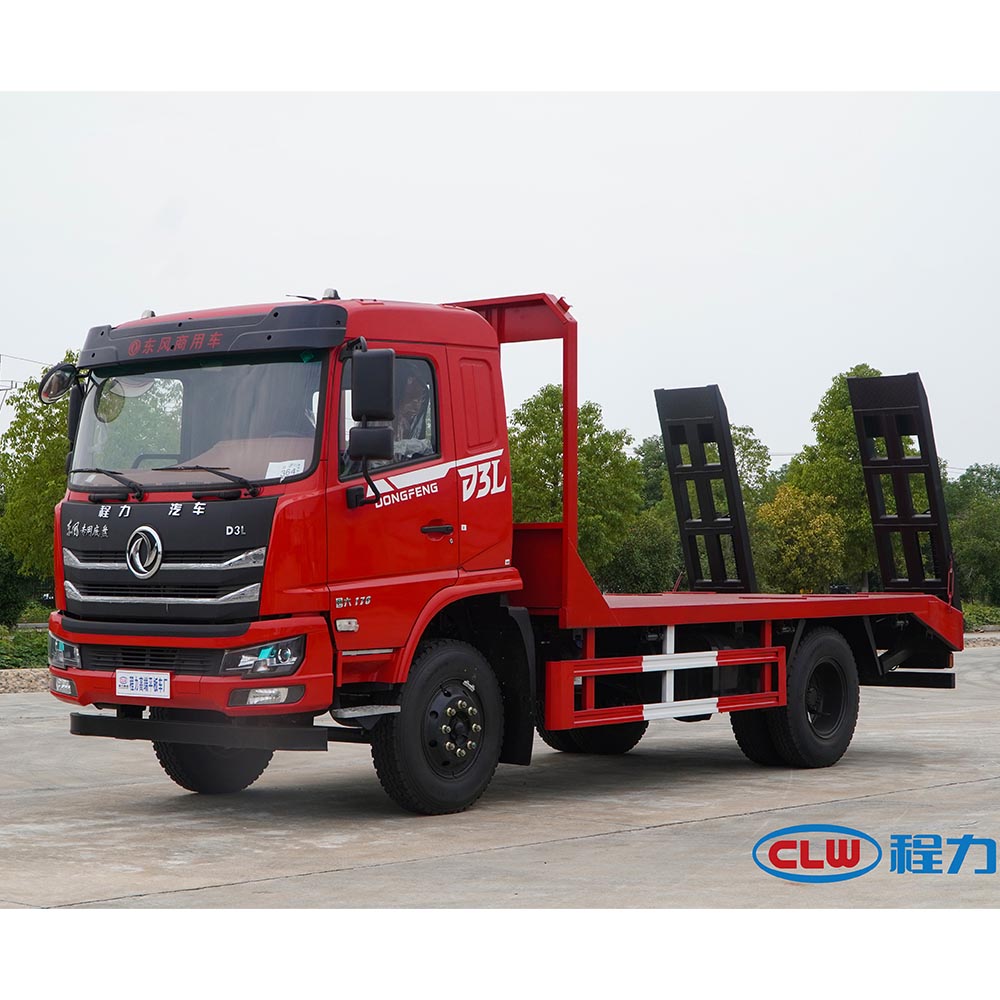
Here’s a quick breakdown:
- Standard Height: Around 48 inches (4 feet)
- Common Applications: Semi-trucks, trailers for large-scale distribution
- Regional Variations: Might exist, but 48 inches is widely accepted
Even with a standard, it’s still important to confirm specific truck and dock compatibility before loading or unloading. This simple check minimizes the risk of accidents and ensures a smoother operation.
It’s like double-checking the recipe before you bake a cake. Makes sense, right?
When “Standard” Isn’t Enough: Dealing with Height Variations
So, we’ve established that 48 inches is the typical loading dock height. What happens when trucks don’t fit the standard? It’s like trying to fit a square peg into a round hole. That’s when the real problem-solving begins!
There are different types of trucks on the road. Smaller delivery trucks, oversized vehicles, and even specialized equipment like the Dongfeng Huashen bulk feed transport truck often have different bed heights. This leads to the need for adaptable solutions.
For example, a small delivery truck might have a bed height of only 36 inches. Trying to load and unload from a 48-inch dock would be difficult and dangerous. Similarly, a heavy-duty truck transporting oversized equipment might have a bed height exceeding the standard. In some instances, flatbed trailers don’t have a covered back, making it difficult to directly load or unload products from the dock. In these cases, specialized equipment is necessary, or items must be loaded from the side or top of the flatbed.
So what can you do to handle these situations?
Bridging the Gap: Dock Levelers to the Rescue
This is where dock levelers, often mentioned in the context of discussing **Standard truck loading dock heights**, enter the picture! These clever devices act like adjustable ramps, bridging the gap between the dock and the truck bed. They come in various shapes and sizes, but the basic principle remains the same: create a safe and smooth transition for forklifts and workers.
Dock levelers are very important in modern loading docks. Without them, it would be nearly impossible to handle the variety of truck heights encountered daily. There are mainly three common types:
- Mechanical Levelers: These are manually operated and are often the most cost-effective option. They use springs and levers to adjust height.
- Hydraulic Levelers: These are electronically controlled and offer smoother, more precise adjustments. They are ideal for high-volume operations.
- Air-Powered Levelers: These use compressed air to raise and lower the platform. They are known for their reliability and low maintenance.
Choosing the right dock leveler depends on factors like budget, frequency of use, and the range of truck bed heights you need to accommodate. It’s a crucial investment that pays off in increased efficiency and safety over time.
Think of dock levelers as the transformers of the loading dock world. They adapt to any situation, ensuring a smooth loading and unloading process every time.
Beyond Levelers: Other Essential Dock Equipment
While dock levelers bridge the height gap, other equipment plays equally vital roles in keeping the loading dock running smoothly. It’s like an orchestra – everyone has to play their their role to make beautiful music!
Here are a few key components:
- Dock Seals and Shelters: These create a tight seal between the truck and the dock opening, protecting goods from weather and preventing energy loss.
- Vehicle Restraints: These secure the truck to the dock, preventing it from moving during loading and unloading. This, in turn, avoids accidents.
- Lighting: Adequate lighting is essential for safety, especially during nighttime operations.
- Communication Systems: Clear communication between dock workers and truck drivers is crucial for coordination, especially when backing up larger loads. A simple two-way radio can fix many headaches.
Each of these components contributes to a safer, more efficient, and more secure loading dock environment.
Think of dock seals and shelters as a warm jacket, vehicle restraints as seatbelts, lighting as a bright flashlight, and communication systems as walkie-talkies. Every tool is important in making sure your dock and product can be successfully secured and loaded/unloaded.
The Future of Loading Docks: Innovations on the Horizon
The world of logistics is constantly evolving, and loading docks are no exception. Innovations are emerging all the time, promising to make the loading and unloading process faster, safer, and more efficient, even exceeding **Standard truck loading dock heights** performance.
Here are a few exciting trends to keep an eye on:
- Automated Loading Systems: Imagine robots handling the entire loading and unloading process! While widespread adoption is still a way off, automated systems are already being used in some facilities to increase speed and reduce labor costs.
- Smart Docks: These use sensors and data analytics to optimize dock operations, tracking truck arrivals, monitoring equipment performance, and identifying potential bottlenecks.
- Green Docks: Sustainability is becoming increasingly important, and loading docks are adapting with energy-efficient lighting, hybrid vehicles and alternative energy sources.
These innovations promise to make loading docks more efficient, worker-friendly and environmentally responsible. The future of logistics is bright!
Think of automated loading systems as self-driving cars for the warehouse, smart docks as a navigation system and green docks as solar panels on your roof. The future is here and it’s very exciting!
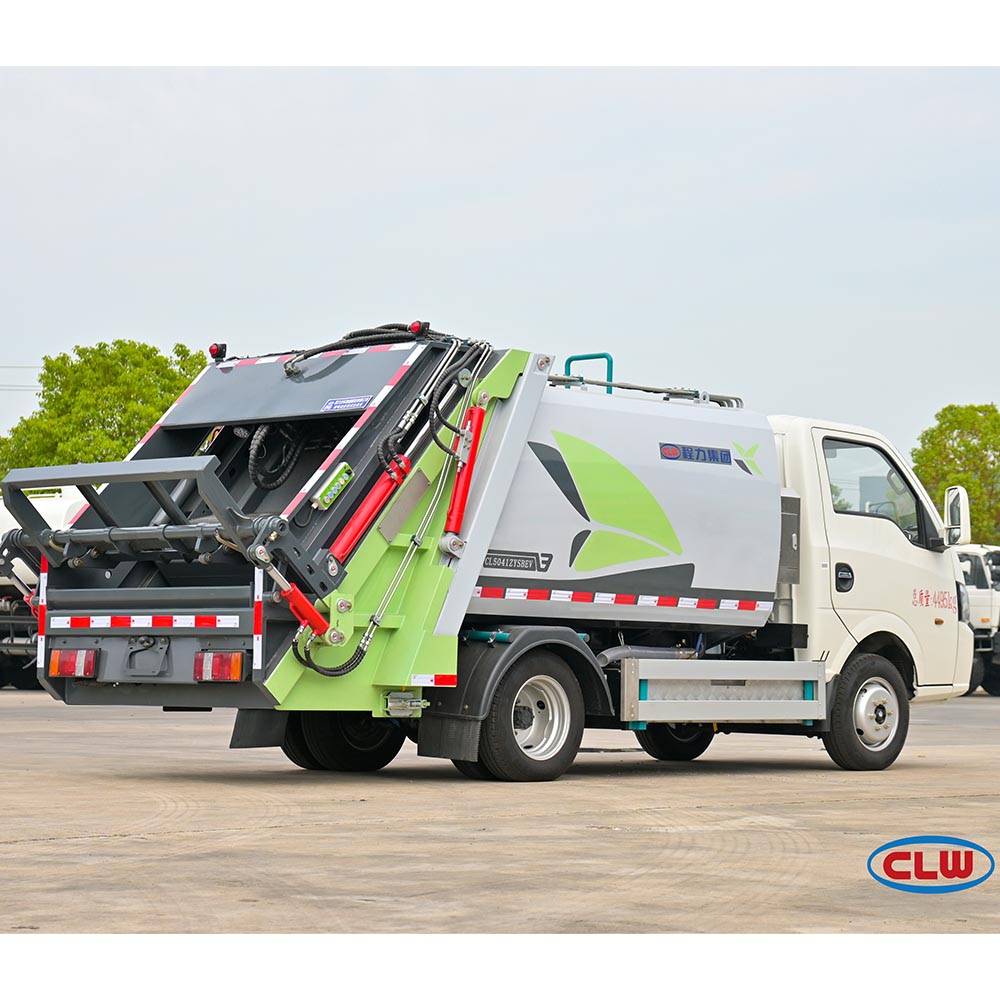
Adapting Docks for Specialized Trucks: A Case Study
Let’s delve into a specific example of how loading docks must adapt to accommodate specialized vehicles. Consider the explosive equipment transport truck. These vehicles, designed to safely carry hazardous materials, often have unique requirements regarding loading and unloading.
Due to the sensitive nature of their cargo, these trucks typically require:
- Designated Loading Areas: Separate areas away from high-traffic zones to minimize risk.
- Specialized Grounding Systems: To prevent static electricity buildup.
- Strict Safety Protocols: Including trained personnel and emergency response plans.
In these cases, standard loading dock heights is only the beginning. The entire loading process must be carefully planned and executed to ensure the safety of both personnel and the surrounding environment. These trucks have different configurations and requirements than the norm. Specialized docks and loading bays must be created to ensure safety above ease-of-use or speed.
Think of adapting docks for specialized trucks as building a custom laboratory for handling sensitive experiments. It requires careful planning, specialized equipment, and rigorous safety measures.
Maintaining Safe Loading Dock Operations: A Checklist
Safety should always be top priority at any loading dock. Neglecting safety doesn’t just increase the risk of accidents; it also impacts productivity and morale.
Here’s a simple checklist to ensure safe operations:
- Regular Equipment Inspections: Check dock levelers, vehicle restraints, and other equipment for wear and tear.
- Proper Training: Ensure all workers are properly trained on safe operating procedures.
- Clear Communication: Establish clear communication protocols between dock workers and truck drivers.
- Adequate Lighting: Maintain sufficient lighting, especially during nighttime hours.
- Enforcement of Safety Rules: Enforce all safety rules and regulations consistently.
By following these guidelines, you can create a safer and more productive loading dock environment for everyone, no matter the **Standard truck loading dock heights**.
Think of this checklist as your pre-flight checklist before takeoff, making sure everything is in order and ready to go.
The Impact of Dock Height on Forklift Operations
Forklifts are the workhorses of any loading dock, and their efficiency is directly impacted by the height of the dock. When the dock height is properly matched to the truck bed, forklifts can move goods quickly and safely. However, a mismatch can lead to problems.
If the dock is too high, forklifts may struggle to climb the incline, increasing the risk of tipping. If the dock is too low, forklifts may bottom out or have difficulty maneuvering. Both situations decrease efficiency and increase the risk of accidents. Forklifts need to be able to seamlessly move product into and out of the truck without risk of tipping over.
Using dock levelers and carefully considering the ground clearance and turning radius of your forklifts can help mitigate these problems. Regular maintenance of forklifts can also contribute to their dependability.
Think of the forklift as a finely tuned race car, needing a smooth track (the dock) to perform at its best. If there are bumps and obstacles (mismatched heights), its performance suffers.
Understanding Legal and Regulatory Considerations
Loading docks are subject to various legal and regulatory requirements aimed at ensuring worker safety and preventing accidents. These regulations, often set by governmental bodies, address everything from dock height to equipment maintenance to worker training.
Common regulatory considerations include:
- OSHA Standards: These cover a wide range of workplace safety issues, including loading dock safety.
- ADA Compliance: Ensuring accessibility for workers with disabilities.
- Local Building Codes: These may specify requirements for dock height and equipment.
Staying informed about and compliant with these regulations is crucial for avoiding fines, liability, and, most importantly, protecting your workers. Consult with safety professionals to ensure your loading dock meets all applicable requirements. You could also hire loading dock specialists.
Think of adhering to legal and regulatory considerations as following the rules of the road. Ignoring them can lead to accidents and hefty fines.
Optimizing Your Loading Dock for Maximum Efficiency
Simply having the correct **Standard truck loading dock heights** is a great starting point, now let’s consider what else we can do to maximize efficiency!. Optimizing your loading dock requires a holistic approach, considering factors such as layout, equipment, and workflow. It’s not just about having the right height. It’s about creating a system that works seamlessly from start to finish.
Here are some tips for optimizing your loading dock:
- Streamline Workflow: Analyze your loading and unloading processes to identify potential bottlenecks.
- Optimize Layout: Ensure adequate space for maneuvering equipment and storing goods.
- Invest in Technology: Consider using automation systems to increase speed and accuracy.
- Train Workers: Train your workers to be more efficient and productive
By implementing these strategies, you can significantly improve your loading dock’s efficiency, reducing costs, improving safety and increasing customer satisfaction.
Think of optimizing your loading dock as tuning up your car for maximum performance. Every adjustment contributes to a smoother, faster ride.
Common Mistakes to Avoid at the Loading Dock
Even with the best equipment and training, mistakes can happen. Knowing the common pitfalls can help you avoid them and keep your loading dock running smoothly.
Here are some frequent mistakes:
- Neglecting Equipment Maintenance:*Regular maintenance is essential to prevent breakdowns and accidents.
- Ignoring Height Discrepancies:Always check truck bed heights and use dock levelers when necessary.
- Poor Communication: Lack of communication can lead to confusion and accidents.
- Rushing the Process: Rushing through loading and unloading increases the risk of mistakes and injuries. Don’t rush… slow and smooth wins the race!
Avoiding these mistakes can significantly improve the safety and efficiency of your loading dock.
Think of avoiding these mistakes as sidestepping potholes on the road. Awareness and caution can prevent a bumpy ride.
If you need more space to move your trucks, consider looking at [Chengli Truck-Mounted Crane Transporter](https://thespecialtrucks.com/chengli-truck-mounted-crane-transporter/).
The Importance of Proper Lighting at the Dock

Don’t underestimate the power of good lighting! Proper lighting at your loading dock is essential for safety and efficiency, particularly during nighttime operations. Dimly lit docks increase the risk of accidents. The workers just can’t see! This, in turn lowers productivity.
Consider these lighting tips:
- Adequate Illumination: Install sufficient lights to illuminate the entire loading area, especially during twilight hours.
- Glare Reduction: Use diffused lighting to minimize glare, which can strain the eyes and reduce visibility.
- Regular Maintenance: Replace burned-out bulbs and clean light fixtures regularly to maintain optimal brightness.
Adequate lighting creates a safer, more productive, and more comfortable work environment. For additional cleaning, considering purchasing a Chengli New Energy – Pure Electric Washing and Sweeping Vehicle.
Think of proper lighting as the sun shining down on your loading dock, making everything clearer and safer.
FAQs About Standard Truck Loading Dock Heights
Let’s answer a few common questions about truck loading dock heights:
What is the ideal height for a loading dock to accommodate most trucks?
The most common standard is around 48 inches (4 feet), but dock levelers enhance versatility.
Are there different height standards for different types of trucks?
Yes, smaller trucks and specialized vehicles may require different dock heights.
How do dock levelers help with varying truck heights?
Dock levelers are adjustable ramps that bridge the gap between the dock and the truck bed, ensuring a smooth transition.
What safety measures should be in place at a loading dock?
Regular equipment inspections, worker training, clear communication, and adequate lighting are essential.
What are some common mistakes to avoid at the loading dock?
Neglecting maintenance, ignoring height discrepancies, and poor communication should all be avoided.
How do I optimize my loading dock for safety?
By using a checklist and taking a planned approach you are best positioned for success.
Conclusion: Mastering the Art of the Loading Dock
Understanding **Standard truck loading dock heights** along with dock levelers, safety measures, and other supporting equipment is a critical element that plays a vital role in keeping our economy moving. From the simple act of matching a truck to a loading dock to making sure your team is adequately trained, everything matters!
By embracing best practices, staying informed about new innovations, and prioritizing safety, you can create a loading dock that is efficient, safe, and ready to meet the challenges of today’s dynamic logistics landscape. You can consider looking at Zero-Emission Street Cleaning: Chengli Electric Sweeper to bring sustainablity to your loading dock too. Happy Trucking!